Prueba e Inspección- Tabletas y Cápsulas
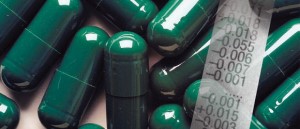
Prueba e Inspección- Tabletas y Cápsulas
Reduzca la inspección visual de las cápsulas incorporando calidad.
Prueba e Inspección
De TABLETAS Y CÁPSULAS
FORMULACIÓN PRODUCCIÓN EMBALAJE
Volumen 6 Número 1
enero de 2008
Reduzca la inspección visual de las cápsulas construyendo calidad en
Empresa JimMoorhead BioCaps
Este artículo analiza algunas limitaciones de la inspección visual de cápsulas y ofrece orientación básica sobre cómo incorporar calidad en el proceso de llenado de cápsulas.
En el transcurso de mis 37 años en el llenado de cápsulas, he instalado maquinaria y he fabricado, llenado, impreso y enfajado cápsulas. En cada uno de estos pasos, a menudo dependía de la inspección visual para garantizar un producto de alta calidad. Pero hay mejores maneras.
Las limitaciones de la inspección visual.
Confiar únicamente en la inspección visual es un error. No solo es tedioso y laborioso, sino que rara vez garantiza un producto terminado de calidad. Nadie puede concentrarse indefinidamente, e incluso los técnicos capacitados que inspeccionan las cápsulas que se mueven sobre una mesa rodante no detectarán algunos productos defectuosos. Una vez realicé una prueba en las instalaciones de un cliente en la que desafié al mejor inspector a encontrar y eliminar las 100 cápsulas defectuosas que había agregado a un lote de 100 000 cápsulas llenas. Mediante una mesa de rodillos, el inspector detectó y extrajo 60 de las 100 cápsulas defectuosas en la primera pasada y otras 27 en una segunda pasada. Eso dejó 13 cápsulas defectuosas que podrían haber llegado al consumidor. Con demasiada frecuencia, las empresas confían en un método visual de verificación en proceso que yo llamo el "método de cazar y picotear". Ahí es donde los técnicos revisan el producto en proceso, buscando cápsulas defectuosas, a veces sin importar cuántas cápsulas inspeccionan o qué tan bien entienden el proceso y la capacidad de la máquina. En la mayoría de los casos, si disminuye la verificación aleatoria en el proceso y la inspección visual, reducirá los costos, la mano de obra y el desperdicio.
Mejora de la inspección William Edwards Deming y Joseph Juran establecieron lo que ahora llamamos control estadístico de procesos (SPC), que adopta un enfoque matemático sistemático para la inspección [1, 2]. En las muchas instalaciones en las que he trabajado, el uso de SPC nos permitió reducir en gran medida la inspección visual.
(Aunque SPC no tiene certificación GMP, encaja bien en un proceso certificado por GMP). Deming usó estadísticas para determinar si un proceso está bajo control al trazar y graficar los resultados, lo que facilitó el reconocimiento de un proceso fuera de control. . Su fórmula es
Calidad = | Resultados del trabajo |
Costos totales |
Cuando la calidad es alta, los costos caen. Cuando los costos son el foco, los costos aumentan y la calidad disminuye. La mayoría de las operaciones de llenado de cápsulas demuestran la precisión de esta fórmula. Por ejemplo, los gerentes de una empresa pueden negarse a comprar un disco dosificador del grosor adecuado para una llenadora de cápsulas de tipo apisonador porque los discos nuevos son caros. Decidir no comprar el disco ahorra dinero a corto plazo, pero luego probablemente le costará más a la empresa porque los técnicos probablemente tendrán que solucionar los problemas de la máquina y/o los gerentes tendrán que retirar algún producto.
Mejorar el proceso de inspección requiere algunas herramientas de muestreo económicas: paletas de muestreo que contienen 100 cápsulas, formularios para registrar los resultados y ladrones que pueden llegar fácilmente a los recipientes de su proceso. Si no puede usar una paleta, use una taza lo suficientemente grande como para contener 100 cápsulas y una pequeña bandeja de plástico. Luego, determine la frecuencia de muestreo (como se explica a continuación) y los límites de calidad aceptables (AQL) para su equipo de llenado específico. Configure la máquina, ejecute algunas cápsulas y, después de alcanzar el peso correcto, inspeccione visualmente el lote. Luego determine el número de defectos, lo que le informa sobre la capacidad de la máquina. Si el producto cumple con los AQL, inicie la ejecución por lotes. A intervalos específicos, tome una muestra, inspecciónela visualmente y registre sus hallazgos. Por ejemplo: “Muestra tomada a las 08:30 horas, cero rajaduras, abolladuras o defectos de unión”. Si el proceso está fuera de control (es decir, demasiados rechazos en una categoría específica), detenga la máquina e identifique y solucione el problema. Además, cada 1 a 2 horas, su personal de control de calidad/garantía de calidad debe tomar muestras del contenedor para determinar si el SPC está funcionando.

Cuando es necesaria una inspección visual, una mesa de rodillos es una herramienta útil que permite al inspector examinar cada parte de la cápsula.
Cortesía de Mendel, East Hanover, NJ
Tamaño y frecuencia de muestreo. Al determinar el tamaño y la frecuencia de muestreo ideales, mire las capacidades de la máquina, no el tamaño del lote o del lote. Para determinar el tamaño de la muestra para el material entrante o los valores de inspección al final del lote, puede usar Military Standard 105E. Tomar una muestra de la raíz cuadrada del lote le permitirá saber si el lote cumple con sus AQL, pero no lo ayudará a determinar la posible causa de los defectos, ya que la fórmula o el relleno de la cápsula pueden ser los culpables. Considere, por ejemplo, una máquina con 12 segmentos y 12 orificios por segmento que tiene un orificio dañado. En esa situación, una muestra de la raíz cuadrada del tamaño del lote no mostrará adecuadamente el nivel de defectos que mostrará una muestra en curso tomada a intervalos oportunos. Cuando está operando una máquina, un factor determinante debe ser la producción por unidad de tiempo (tasa). Dado que muchos fabricantes de suplementos nutricionales utilizan llenadoras de cápsulas de varias marcas y modelos, tenga en cuenta que las llenadoras tendrán diferentes capacidades y, en última instancia, diferentes velocidades. Otro factor determinante es cuántas cápsulas caben en los segmentos, bujes o anillos de llenado de su llenador de cápsulas. ¿Los rechazos son causados por la formulación, las cápsulas, la alineación o la configuración? Un tamaño de muestra aceptable y una frecuencia de muestreo pueden ayudar a identificar si el problema es un segmento, un buje, un orificio o toda la configuración. Una regla general para la frecuencia de muestreo es inspeccionar 100 cápsulas cada 30 minutos. Si el inicio transcurre sin problemas, es probable que haya pocos defectos más adelante, a menos que una fórmula problemática obstaculice el funcionamiento de la máquina o cambie de proveedor de cápsulas o de cápsulas.
Los AQL generalmente clasifican los defectos como críticos, mayores o menores. Cada una de estas clasificaciones tiene un AQL de "aprobado" o "rechazado" basado en sus especificaciones internas. Si la llenadora de cápsulas crea un defecto en el producto que requiere ajustes de la máquina y un tiempo de inactividad considerable para corregirlo, entonces aumentará el costo de producción del producto. En algunos casos en los que los productos nutricionales no cumplen con las capacidades de la máquina, será necesaria una clasificación visual.
Gestión de la calidad
Juran acuñó el Principio de Pareto, que establece que el 80 % de los problemas se debe al 20 % de las causas habituales, que en este caso podría ser una formulación defectuosa o una configuración incorrecta [2, 3]. Según Juran, la gestión de la calidad comienza desde arriba. Por lo tanto, los gerentes de nivel superior e intermedio deben recibir capacitación en gestión de la calidad mediante la planificación de la calidad, el control de la calidad y la mejora de la calidad. Planeación de calidad. Compre las cápsulas, los materiales y las piezas de la máquina adecuados para optimizar la producción. Los gerentes deben comprender cómo funciona la máquina llenadora y el proceso general para poder seleccionar los componentes compatibles con su equipo, y los formuladores deben determinar si un producto realmente puede funcionar en la máquina. A menudo uso un slug tester, que consta de un dinamómetro y una cavidad con un diámetro igual al del orificio del disco dosificador.

Cuando es necesaria una inspección visual, una mesa de rodillos es una herramienta útil que permite al inspector examinar cada parte de la cápsula.
Cortesía de Mendel, East Hanover, NJ
El probador ayuda a determinar el grosor que debe tener el disco y si la formulación formará un bache, se liberará del disco correctamente y contribuirá a que la máquina funcione limpiamente con un buen control del peso. Dependiendo del estilo de la máquina, pueden ser necesarias diferentes pruebas. Control de calidad. Realice verificaciones durante el proceso para detectar defectos físicos y peso fuera de especificación, luego registre los resultados en un cuadro o gráfico. De esa manera, cuando un proceso se desvía, puede notarlo rápidamente y realizar cambios. Mejora de la calidad. Escuche a sus mejores recursos: sus empleados. Entienden las fórmulas, las piezas y las reparaciones necesarias para que el proceso de llenado de cápsulas funcione al más alto nivel. Lo escucho todo el tiempo: “Le dije a mis gerentes sobre este problema, pero me ignoraron”. Mientras tanto, los mismos gerentes escuchan con entusiasmo a los técnicos externos y reparan personas porque son los presuntos expertos. Pero he aprendido que los empleados que ejecutan el proceso todos los días también poseen una gran cantidad de conocimientos valiosos. De hecho, mi experiencia en este tema proviene de muchos años de trabajo con técnicos de primera línea. También puedes pedir consejo a tus proveedores y buscar tips en publicaciones como esta. Hay una razón por la que los fabricantes de equipos colocan pasadores de apisonamiento en su máquina de apisonamiento: ¡para que se utilicen! El noventa por ciento de las máquinas de bateo que veo están bateando incorrectamente o no batean en absoluto. Las tomas de vacío y otros dispositivos también se instalan por una razón, así que no los desconecte. Cuando su máquina automática está configurada correctamente, utiliza un disco de dosificación del tamaño adecuado y ejecuta una fórmula compatible, eliminará la mayoría de las inspecciones visuales y los desperdicios.
La instalación de equipos de inspección en línea es otra forma de mejorar la calidad del producto. Estos dispositivos pueden eliminar cápsulas partidas, trituradas y vacías y fragmentos de cápsulas. En la mayoría de las máquinas de llenado de cápsulas, la formulación y el volumen de llenado suelen ser las causas principales de los defectos físicos. Si conoce las capacidades de la máquina y la cápsula y formula su producto para cumplir con estas capacidades, reducirá los costos, la mano de obra y el desperdicio. Fiel a la fórmula de Deming, cuando pone calidad en el producto, entregará calidad al cliente.
términos y condiciones
Referencias
1. Deming, WE 1986. Fuera de la crisis. Cambridge, MA: MIT Press.
2. Juran, J. 1951. Manual de control de calidad. Nueva York, Nueva York: McGraw-Hill.
3. Juran, J. 1970. Planificación y análisis de calidad. Nueva York, Nueva York: McGraw-Hill.
JimMoorhead es director de servicio técnico en BioCaps Enterprise, 9698 Telstar Avenue, Suite 309, El Monte, CA 91731.
tel. 626 545 2862, fax 626 575 2866. Web:
www.biocaps.net. Moorhead tiene 23 años de experiencia como representante de servicio técnico para varios fabricantes de cápsulas.