Test et inspection-comprimés et capsules
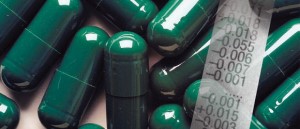
Test et inspection-comprimés et capsules
Réduisez l'inspection visuelle des gélules en intégrant la qualité.
Essai et inspection
À partir de COMPRIMÉS & CAPSULES
FORMIULATION PRODUCTION CONDITIONNEMENT
Tome 6 Numéro 1
janvier 2008
Réduisez l'inspection visuelle des capsules en construisant la qualité dans
JimMoorhead BioCaps Entreprise
Cet article traite de certaines limites de l'inspection visuelle des gélules et offre des conseils de base sur la façon d'intégrer la qualité dans votre processus de remplissage de gélules.
Au cours de mes 37 années de remplissage de gélules, j'ai installé des machines et fabriqué, rempli, imprimé et bagué des gélules. À chacune de ces étapes, je me fiais souvent à une inspection visuelle pour garantir un produit de haute qualité. Mais il existe de meilleurs moyens.
Les limites de l'inspection visuelle
Se fier uniquement à l'inspection visuelle est une erreur. Non seulement c'est fastidieux et laborieux, mais cela garantit rarement un produit fini de qualité. Personne ne peut se concentrer indéfiniment, et même les techniciens formés inspectant les capsules se déplaçant sur une table à rouleaux ne verront pas certains produits défectueux. Une fois, j'ai effectué un test chez un client au cours duquel j'ai mis au défi le meilleur inspecteur de trouver et de retirer les 100 capsules défectueuses que j'avais ajoutées à un lot de 100 000 capsules remplies. À l'aide d'une table à rouleaux, l'inspecteur a détecté et retiré 60 des 100 capsules défectueuses lors du premier passage et 27 autres lors d'un second passage. Cela a laissé 13 capsules défectueuses qui auraient pu atteindre le consommateur. Trop souvent, les entreprises s'appuient sur une méthode visuelle de vérification en cours de processus que j'appelle la «méthode de chasse et de picorage». C'est là que les techniciens parcourent le produit en cours de fabrication, cherchant à trouver des capsules défectueuses, parfois sans tenir compte du nombre de capsules qu'ils inspectent ou de leur compréhension du processus et des capacités de la machine. Dans la plupart des cas, si vous réduisez ces vérifications aléatoires en cours de processus et les inspections visuelles, vous réduisez les coûts, la main-d'œuvre et les déchets.
Améliorer l'inspection William Edwards Deming et Joseph Juran ont établi ce que nous appelons aujourd'hui le contrôle statistique des processus (SPC), qui adopte une approche systématique et mathématique de l'inspection [1, 2]. Dans les nombreuses installations où j'ai travaillé, l'utilisation de SPC nous a permis de réduire considérablement l'inspection visuelle.
(Bien que SPC ne soit pas certifié GMP, il s'intègre bien dans un processus certifié GMP.) Deming a utilisé des statistiques pour déterminer si un processus est sous contrôle en traçant et en traçant les résultats, ce qui a facilité la reconnaissance d'un processus hors de contrôle. . Sa formule est
Qualité = | Résultats de travail |
Coûts totaux |
Lorsque la qualité est élevée, les coûts baissent. Lorsque les coûts sont au centre des préoccupations, les coûts augmentent et la qualité diminue. La plupart des opérations de remplissage de capsules prouvent l'exactitude de cette formule. Par exemple, les responsables d'une entreprise peuvent hésiter à acheter un disque de dosage de l'épaisseur appropriée pour un remplisseur de gélules de type tassage car les nouveaux disques sont chers. Décider de ne pas acheter le disque permet d'économiser de l'argent à court terme, mais plus tard, cela coûtera probablement plus cher à l'entreprise car les techniciens devront probablement dépanner la machine et/ou les responsables devront rappeler certains produits.
L'amélioration du processus d'inspection nécessite quelques outils d'échantillonnage peu coûteux : des palettes d'échantillonnage pouvant contenir 100 capsules, des formulaires pour enregistrer les résultats et des voleurs qui peuvent facilement atteindre vos cuves de traitement. Si vous ne pouvez pas utiliser de palette, utilisez une tasse assez grande pour contenir 100 capsules et un petit plateau en plastique. Ensuite, déterminez la fréquence d'échantillonnage (comme indiqué ci-dessous) et les limites de qualité acceptables (AQL) pour votre équipement de remplissage spécifique. Configurez la machine, faites fonctionner quelques capsules et, une fois le poids correct atteint, inspectez visuellement le lot. Déterminez ensuite le nombre de défauts, qui vous renseigne sur les capacités de la machine. Si le produit respecte les NQA, démarrez l'exécution par lots. À des intervalles spécifiés, prélevez un échantillon, inspectez-le visuellement et notez vos résultats. Par exemple : "Échantillon prélevé à 08h30, zéro fente, bosse ou défaut d'assemblage." Si le processus est hors de contrôle (c.-à-d. trop de rejets dans une catégorie spécifiée), arrêtez la machine et identifiez et corrigez le problème. De plus, toutes les 1 à 2 heures, votre personnel QC/QA doit prélever des échantillons de vol du conteneur pour déterminer si le SPC fonctionne.

Lorsqu'une inspection visuelle est nécessaire, une table à rouleaux est un outil utile qui permet à l'inspecteur d'examiner chaque partie de la capsule.
Avec l'aimable autorisation de Mendel, East Hanover, NJ
Taille et fréquence d'échantillonnage. Lorsque vous déterminez la taille et la fréquence d'échantillonnage idéales, examinez les capacités de la machine, et non la taille du lot ou du lot. Pour déterminer la taille d'échantillonnage pour les matières entrantes ou les valeurs d'inspection de fin de lot, vous pouvez utiliser la norme militaire 105E. Prendre un échantillon de racine carrée du lot vous permettra de savoir si le lot répond à vos NQA, mais cela ne vous aidera pas à déterminer la cause potentielle des défauts, car la formule ou le remplisseur de gélule peut être à blâmer. Considérons, par exemple, une machine avec 12 segments et 12 trous par segment qui a un trou endommagé. Dans cette situation, un échantillon de racine carrée de la taille du lot ne montrera pas de manière adéquate le niveau de défaut qu'un échantillon continu prélevé à intervalles réguliers le fera. Lorsque vous utilisez une machine, un facteur déterminant doit être la sortie par unité de temps (taux). Étant donné que de nombreux fabricants de suppléments nutritionnels utilisent des remplisseurs de gélules de différentes marques et modèles, gardez à l'esprit que les remplisseurs auront des capacités différentes et finalement des taux différents. Un autre facteur déterminant est le nombre de gélules qui rentrent dans les segments, les bagues ou les anneaux de remplissage de votre remplisseuse de gélules. Les rejets sont-ils dus à la formulation, aux capsules, à l'alignement ou à la configuration ? Une taille d'échantillon et une fréquence d'échantillonnage acceptables peuvent aider à déterminer si le problème concerne un segment, une douille, un trou ou l'ensemble de la configuration. Une règle de base pour la fréquence d'échantillonnage est d'inspecter 100 capsules toutes les 30 minutes. Si le démarrage se passe bien, il est probable qu'il y aura peu de défauts plus tard, à moins qu'une formule problématique n'entrave le fonctionnement de la machine ou que vous ne changiez de fournisseur de capsules ou de capsules.
Les NQA classent généralement les défauts comme critiques, majeurs ou mineurs. Chacune de ces classifications a un NQA « réussi » ou « rejeté » basé sur vos spécifications internes. Si le remplisseur de gélules crée un défaut de produit qui nécessite des ajustements de la machine et des temps d'arrêt importants pour être corrigé, le coût de production du produit augmentera. Dans certains cas où les produits nutritionnels ne répondent pas aux capacités de la machine, un tri visuel sera nécessaire.
Gestion de la qualité
Juran a inventé le principe de Pareto, qui stipule que 80 % des problèmes sont causés par 20 % des causes habituelles, qui dans ce cas pourraient être une formulation erronée ou une mauvaise configuration [2, 3]. Selon Juran, la gestion de la qualité commence au sommet. Par conséquent, les cadres supérieurs et intermédiaires doivent être formés à la gestion de la qualité en utilisant la planification de la qualité, le contrôle de la qualité et l'amélioration de la qualité. Planification de qualité. Achetez les bonnes capsules, matériaux et pièces de machine pour optimiser la production. Les responsables doivent comprendre le fonctionnement de la machine de remplissage et du processus global afin de pouvoir sélectionner des composants compatibles avec leur équipement, et les formulateurs doivent déterminer si un produit peut réellement fonctionner sur la machine. J'utilise souvent un slug tester, qui comprend un dynamomètre et une cavité de diamètre égal à celui du trou du disque doseur.

Lorsqu'une inspection visuelle est nécessaire, une table à rouleaux est un outil utile qui permet à l'inspecteur d'examiner chaque partie de la capsule.
Avec l'aimable autorisation de Mendel, East Hanover, NJ
Le testeur aide à déterminer l'épaisseur du disque et si la formulation formera un bouchon, se dégagera correctement du disque et contribuera à un fonctionnement propre de la machine avec un bon contrôle du poids. Selon le type de machine, différents tests peuvent être nécessaires. Contrôle de qualité. Effectuez des vérifications en cours de fabrication pour détecter les défauts physiques et le poids hors spécifications, puis enregistrez les résultats dans un tableau ou un graphique. De cette façon, lorsqu'un processus s'égare, vous pouvez le remarquer rapidement et apporter des modifications. Amelioration de la qualite. Écoutez vos meilleures ressources : vos employés. Ils comprennent les formules, les pièces et les réparations nécessaires pour que le processus de remplissage des gélules fonctionne au plus haut niveau. Je l'entends tout le temps : "J'ai parlé de ce problème à mes managers, mais ils m'ont ignoré." Pendant ce temps, les mêmes gestionnaires écoutent avec impatience les techniciens extérieurs et les réparateurs parce qu'ils sont les experts présumés. Mais j'ai appris que les employés qui exécutent le processus au quotidien possèdent également de nombreuses connaissances précieuses. En fait, mon expertise sur ce sujet découle de plusieurs années de travail avec des techniciens de première ligne. Vous pouvez également demander conseil à vos fournisseurs et rechercher des conseils dans des publications comme celle-ci. Il y a une raison pour laquelle les fabricants d'équipements mettent des goupilles de bourrage sur votre machine de type bourrage - pour qu'elle soit utilisée ! Quatre-vingt-dix pour cent des machines de type bourrage que je vois bourrent mal ou ne bourrent pas du tout. Les prises de vide et autres appareils sont également installés pour une raison, alors ne les déconnectez pas. Lorsque votre machine automatique est configurée correctement, utilise un disque de dosage de taille appropriée et exécute une formule compatible, vous éliminerez la plupart des inspections visuelles et des déchets.
L'installation d'équipements d'inspection en ligne est un autre moyen d'améliorer la qualité des produits. Ces dispositifs peuvent éliminer les capsules fendues, écrasées et vides et les fragments de capsule. Sur la plupart des machines de remplissage de gélules, la formulation et le volume de remplissage sont généralement les principales causes de défauts physiques. Si vous connaissez les capacités de la machine et des capsules et que vous formulez votre produit pour répondre à ces capacités, vous réduirez les coûts, la main-d'œuvre et les déchets. Fidèle à la formule de Deming, lorsque vous mettez de la qualité dans le produit, vous livrez de la qualité au client.
CGV
Références
1. Deming, WE 1986. Sortir de la crise. Cambridge, Massachusetts : MIT Press.
2. Juran, J. 1951. Manuel de contrôle de la qualité. New York, New York : McGraw-Hill.
3. Juran, J. 1970. Planification et analyse de la qualité. New York, New York : McGraw-Hill.
JimMoorhead est directeur du service technique chez BioCaps Enterprise, 9698 Telstar Avenue, Suite 309, El Monte, CA 91731.
Tél. 626 545 2862, fax 626 575 2866. Site Internet :
www.biocaps.net. Moorhead a 23 ans d'expérience en tant que représentant du service technique pour un certain nombre de fabricants de capsules.